Adiabatic CSTR Reactors Integrated with Glass-Fused-to-Steel Tanks for Energy-Efficient Digestion
In the chemical industry, optimizing energy usage and enhancing operational stability are central to sustainable development. Adiabatic Continuous Stirred Tank Reactors (CSTRs), especially when integrated with Glass-Fused-to-Steel (GFS) tanks, are proving to be a game-changing solution for efficient biochemical and chemical digestion processes. As a leading manufacturer with over 30 years of experience in bolted storage solutions, Center Enamel provides customized CSTR systems that meet the demands of energy conservation, corrosion resistance, and long-term operational reliability. Our CSTRs are widely recognized for their compatibility with various chemical industry processes, making them an essential component in anaerobic digestion systems, biogas projects, and industrial waste treatment.
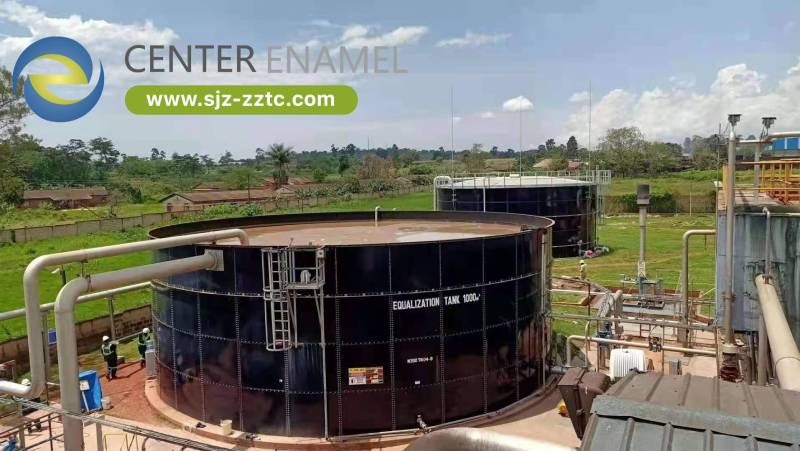
Key Advantages of Adiabatic CSTR Reactors with GFS Tanks
Stable Temperature Control: Adiabatic CSTRs are designed to minimize heat loss, allowing chemical reactions to maintain a consistent internal temperature. This is especially crucial in digestion processes where heat conservation enhances reaction rates and gas yield.
Glass-Fused-to-Steel Durability: The GFS tanks used in Center Enamel’s CSTR systems feature a dual-layer design—glass coating fused to steel—which ensures exceptional corrosion resistance, chemical inertness, and structural integrity.
Low Maintenance Requirements: The smooth, low-porosity surface of the GFS tanks reduces residue buildup, significantly lowering cleaning frequency and maintenance downtime.
High Operational Safety: The enclosed nature of the system and the chemical resistance of GFS tanks reduce the risk of leaks and contamination, ensuring safe operation in harsh chemical environments.
Customizable Design: Center Enamel offers modular design options for tank volume, mixer types, heating methods, and insulation, enabling flexible adaptation to specific industry needs.
Importance of Adiabatic CSTR Reactors in the Chemical Industry
Efficient Chemical Digestion: Adiabatic CSTRs are ideal for applications requiring continuous chemical reactions such as hydrolysis, neutralization, and fermentation. Their ability to maintain consistent thermal conditions supports efficient process kinetics.
Waste-to-Energy Conversion: In chemical manufacturing, byproducts and organic wastes are increasingly being treated using anaerobic digestion. The integration of adiabatic control in CSTRs boosts methane production, aiding in the recovery of valuable biogas.
Pollution Control Compliance: Industries benefit from using these reactors to meet strict environmental regulations regarding hazardous waste treatment, effluent discharge standards, and volatile emissions.
Enhancing Process Scalability: The modularity and capacity range of CSTR systems make them suitable for both pilot projects and full-scale industrial operations, supporting industry growth and innovation.
Design and Application Considerations in Industrial Use
When implementing adiabatic CSTR reactors in the chemical industry, several factors must be carefully considered to maximize efficiency and performance:
Thermal Insulation Systems: Proper insulation is vital to preserving the adiabatic nature of the system. Center Enamel offers advanced insulation materials to prevent heat loss and reduce energy input costs.
Agitation Mechanisms: Selecting the right type of stirrer (e.g., mechanical, hydraulic, or pneumatic) affects mixing efficiency and reaction homogeneity. Our engineering team tailors mixing solutions based on viscosity and reaction type.
Chemical Compatibility: The interior glass coating of GFS tanks is resistant to a wide range of aggressive chemicals (acids, alkalis, solvents), ensuring long service life in corrosive environments.
Automated Monitoring and Control: Integration with SCADA systems and real-time sensors allows for continuous monitoring of parameters such as pH, temperature, and pressure, enabling timely process adjustments.
Site Layout and Space Optimization: Center Enamel designs its CSTR systems for efficient use of available land, minimizing footprint without compromising capacity or functionality.
Why Choose Center Enamel for CSTR Reactor Solutions
Proven Track Record: Center Enamel has exported GFS tanks and integrated CSTR solutions to over 100 countries, including the USA, Canada, Australia, UAE, and Brazil. Our systems are trusted by global clients in the chemical, environmental, and energy sectors.
Certified Quality: Our GFS tanks and CSTR systems comply with international standards, including ISO 9001, ISO 28765, NSF/ANSI 61, AWWA D103-09, and EN1090. We also hold over 200 enameling technology patents.
Full-Service Engineering: From initial consultation and project design to manufacturing, installation, and after-sales service, Center Enamel provides comprehensive EPC technical support.
Innovation in Design: We continuously invest in R&D and manufacturing upgrades to offer customers advanced tank technologies, including energy-efficient coatings, smart tank monitoring, and AI-based process optimization.
Sustainability Commitment: Our reactors contribute to global sustainability by facilitating clean energy production and industrial waste reduction, aligning with worldwide goals for carbon neutrality and circular economy.
With a vision to empower the chemical industry through innovation and efficiency, Center Enamel’s adiabatic CSTR reactors integrated with GFS tanks represent the ideal solution for energy-efficient digestion and chemical treatment processes. Our commitment to quality, performance, and sustainability ensures that every project we deliver is built to exceed expectations.