Advanced IC Reactor Systems for Fermentation Wastewater Treatment
In recent years, the industrial fermentation sector has seen exponential growth across various sub-industries, including pharmaceuticals, alcohol production, biofuels, enzymes, and food additives. Along with this expansion comes a pressing need to manage fermentation wastewater, which is often characterized by high concentrations of organic matter, volatile fatty acids, and complex nutrients. As industries look for sustainable and cost-effective treatment options, IC Reactors (Internal Circulation Reactors) emerge as one of the most efficient anaerobic treatment technologies. When developed and implemented by a trusted IC reactor manufacturer, such as Shijiazhuang Zhengzhong Technology Co., Ltd. (Center Enamel), these systems become reliable and long-lasting assets for wastewater management.
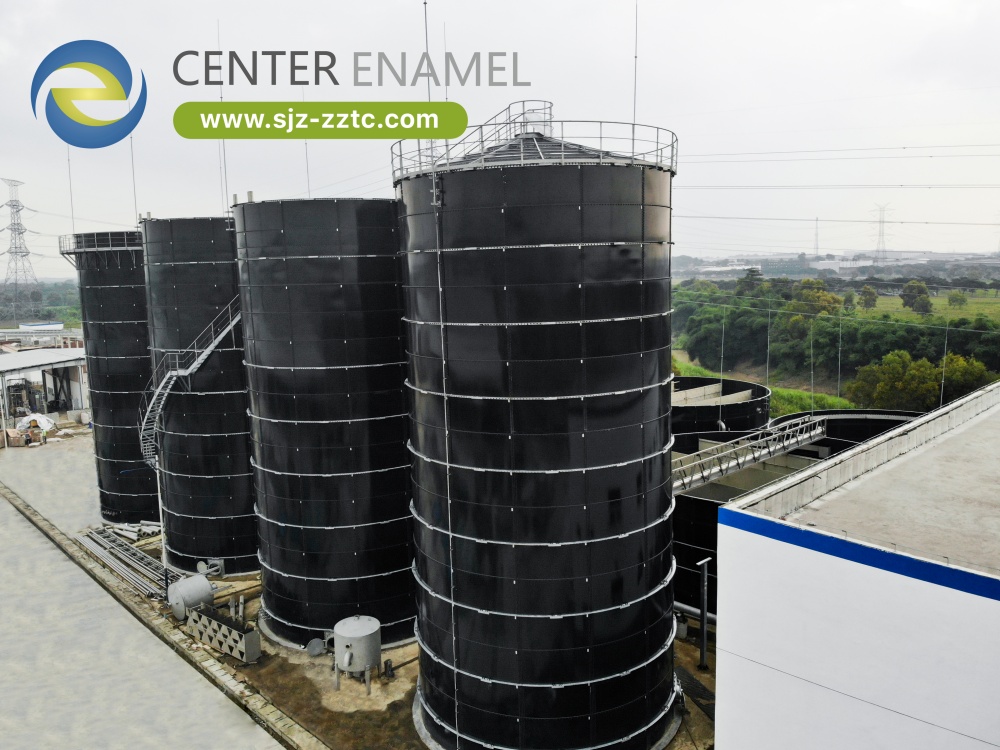
With more than 30 years of experience in the design and manufacture of high-performance anaerobic digestion systems, Center Enamel has become a global leader in wastewater treatment solutions. The company provides advanced IC reactors combined with precision-engineered tank systems for fermentation and other high-COD industrial wastewater treatment applications. Known for integrating advanced technology with robust structural materials, Center Enamel delivers turnkey projects in over 90 countries across six continents.
Why IC Reactors Are Ideal for Fermentation Wastewater Treatment
IC Reactors have revolutionized the anaerobic treatment landscape by offering enhanced bioconversion rates, compact design, and high energy recovery through biogas generation. Their structural and operational advantages make them uniquely suited for the treatment of fermentation wastewater, which can include a mix of sugars, ethanol residues, yeast by-products, and nutrient-rich effluents.
Key Advantages:
High Organic Load Capacity
IC reactor can treat wastewater with relatively high COD concentration. This makes them ideal for fermentation-based industries such as breweries, distilleries, and amino acid production plants.
Two-Stage Anaerobic Digestion
The IC reactor’s vertical structure accommodates two anaerobic digestion stages. In the lower reactor zone, active sludge is maintained for hydrolysis and acidogenesis. In the upper stage, methane production occurs, resulting in higher biogas output and more stable effluent quality.
Efficient Sludge Management
IC reactors produce significantly lower sludge volumes due to optimized microbial retention and internal circulation, minimizing sludge disposal costs and environmental impact.
Rapid Start-Up and Recovery
The reactor's structure supports a fast accumulation of biomass, reducing start-up time to just a few weeks. In the event of shock loading or system interruption, recovery is quicker than with conventional reactors.
Biogas Utilization
The high biogas production from fermentation wastewater can be collected and reused as fuel for Combined Heat and Power (CHP) systems, offsetting energy costs and contributing to a circular economy.
Reduced Odor and Greenhouse Gas Emissions
With sealed construction and efficient gas collection systems, IC reactors minimize odor emissions and greenhouse gases, improving workplace conditions and sustainability compliance.
Role of IC Reactors in Global Fermentation Industry Wastewater Projects
Center Enamel’s IC reactor systems have been successfully deployed in fermentation plants worldwide, addressing diverse wastewater characteristics and treatment objectives. Below are examples from specific fermentation sub-sectors where IC reactors have had a transformative impact.
1. Pharmaceutical Fermentation Plants
Pharmaceutical production, especially antibiotics and enzymes, generates highly variable wastewater with complex chemical structures. IC reactors, due to their robust microbial communities and internal mixing design, can adapt to these fluctuations. Center Enamel’s modular IC reactor units in India are used to treat effluent from penicillin and streptomycin production.
2. Amino Acid and Organic Acid Production
Industries producing lysine, glutamic acid, or citric acid release wastewater with high organic acid loads and low pH. IC reactors accommodate this by pre-neutralization and tailored biomass retention strategies. Center Enamel has designed systems in China and South Korea specifically for such applications, achieving high treatment efficiency and process stability.
3. Biofuel and Bioplastics Fermentation
Wastewater from ethanol and bioplastic production contains volatile fatty acids, glycerol, and by-products of fermentation. These are excellent substrates for anaerobic digestion. IC reactors by Center Enamel have been implemented in bioethanol plants to reduce treatment costs and increase energy self-sufficiency through methane recovery.
Considerations for Selecting an IC Reactor Manufacturer
When planning a fermentation wastewater treatment project, choosing the right IC reactor manufacturer is critical to project success. Center Enamel distinguishes itself through the following key strengths:
1. Custom Design Expertise
Each IC reactor is customized based on wastewater characteristics, treatment objectives, and site limitations. Center Enamel employs advanced modeling software and laboratory-scale trials to ensure optimal reactor sizing and performance.
2. Material Innovation: Fusion-Bonded Epoxy Tanks
Center Enamel’s reactors are paired with fusion bonded epoxy (FBE) coated steel tanks. These tanks offer superior resistance to corrosion, pH fluctuations, and high internal pressures. Their bolted modular design enables faster installation and easy future expansion.
3. Integrated Engineering and Automation
The company provides complete systems, including feeding systems, gas holders, mixing units, sludge handling, and SCADA automation. Real-time monitoring ensures stable performance even under variable loading.
4. Global Project Implementation
Center Enamel’s IC reactor systems have been successfully deployed in more than 100 countries. From Africa and Southeast Asia to Europe and Latin America, their experience spans across cultures, regulations, and climate conditions.
5. Certifications and Compliance
All systems conform to international standards, including ISO9001, ISO14001, ISO45001, and NSF/ANSI 61 for tank coatings. IC reactors are designed according to ASME, AWWA, and GB engineering codes for structural and process safety.
Enhancing Reactor Efficiency with Fusion-Bonded Epoxy Tank Technology
The combination of IC reactors with fusion-bonded epoxy tanks offers unmatched durability and process stability for fermentation wastewater treatment.
Key Benefits of Epoxy-Coated Tanks:
Chemical Resistance: The internal surface resists corrosion caused by organic acids and cleaning agents commonly found in fermentation effluents.
Thermal Insulation: Paired with outer insulation layers, epoxy-coated tanks help maintain optimal mesophilic or thermophilic digestion temperatures
Low Maintenance: Smooth epoxy surfaces prevent scaling and biofilm formation, ensuring consistent reactor performance with minimal maintenance.
Modularity and Scalability: Systems can be easily upgraded or relocated, making them ideal for growing fermentation plants or multi-site operations.
Future Trends and Sustainable Impact
As fermentation industries move toward green production and net-zero goals, IC reactors offer an ideal solution for waste-to-energy conversion, water recycling, and carbon footprint reduction. Center Enamel continues to invest in R&D to optimize reactor designs for higher loading rates, lower energy input, and improved nutrient recovery.
Emerging trends include:
AI-Powered Process Optimization
Machine learning algorithms are being incorporated into control systems to predict reactor performance and optimize feed dosing.
Integration with Aerobic Polishing
In some cases, anaerobic IC reactors are followed by MBR (Membrane Bioreactor) or SBR (Sequencing Batch Reactor) units to meet ultra-low discharge limits.
Nutrient Recovery Systems
New technologies are being developed to recover nitrogen and phosphorus from fermentation wastewater for reuse in agriculture or industry.