Continuous CSTR Reactor Operation with Enamel Assembly Tanks for Scalable Waste Treatment
In the field of industrial and municipal wastewater treatment, Continuous Stirred Tank Reactors (CSTRs) are a foundational technology—especially in anaerobic digestion systems, where the consistent breakdown of organic materials is key to producing renewable energy and reducing pollution. When paired with high-quality enamel assembly tanks, these reactors offer an ideal combination of chemical resistance, mechanical durability, and operational scalability. Center Enamel, a globally recognized provider of wastewater treatment solutions and the leading manufacturer of enamel tanks in China, delivers cutting-edge CSTR reactor systems that support continuous, scalable waste treatment across various industries, including chemical processing, agriculture, and public utilities.
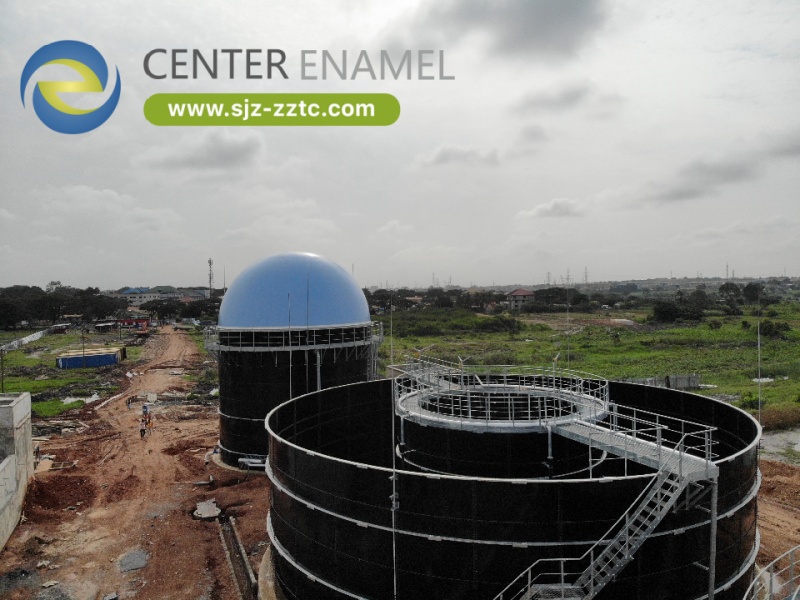
Advantages of Continuous CSTR Reactors with Enamel Tanks
Continuous CSTR systems paired with enamel-assembled tanks bring a wide range of technical and operational advantages to the waste treatment sector.
Uniform Mixing and Digestion Efficiency
CSTR reactors maintain a constant mixing action through mechanical stirrers, ensuring uniform distribution of temperature, pH, and substrate throughout the tank. This prevents the formation of dead zones, enhances digestion efficiency, and leads to more consistent biogas production in anaerobic applications.
Stable Operating Conditions
With continuous input and output flow, these reactors avoid shock loading and maintain steady-state biological conditions. This stability is essential for preserving the health of microbial populations, especially in sensitive chemical wastewater treatment.
High Volatile Solids Reduction
CSTR systems are highly effective at reducing volatile solids in sludge, making them suitable for treating high-strength organic wastewater with a high COD or BOD load.
Modular Scalability
Enamel tanks used in the assembly of CSTRs allow for modular expansion. Projects can begin on a small scale and grow as demand increases, with minimal structural disruption.
Corrosion Resistance and Longevity
Glass-Fused-to-Steel (GFS) tanks, or enamel-assembled tanks, have a high resistance to corrosion, chemical attack, and extreme temperatures. This significantly extends the operational life of the reactor, even under aggressive wastewater conditions.
Quick Installation and Lower Maintenance Costs
Thanks to their factory-baked enamel panels and bolted construction, these tanks are easy to transport and install. Maintenance is also simpler due to the non-stick, easy-to-clean enamel surfaces.
Importance of CSTR Reactor Systems in Waste Treatment Industry Applications
In countries undergoing rapid industrialization and urbanization, continuous CSTR reactors are a vital part of sustainable waste treatment and renewable energy strategies. Their importance in various sectors is clear:
Municipal Wastewater Treatment
Urban centers generate large volumes of sewage and sludge daily. CSTR systems with enamel tanks provide reliable performance in the digestion of municipal sludge, helping reduce landfill waste and recover biogas energy.
Agricultural Waste Management
Livestock farms and agricultural facilities often face challenges in treating manure and organic residues. CSTR reactors provide an effective solution for breaking down complex organic waste and reducing pathogen loads while generating biogas that can be reused on-site for heating or electricity.
Industrial Wastewater Processing
Chemical manufacturing, food processing, and paper production generate high-load wastewater that requires consistent biological treatment. Continuous CSTR operation ensures reliable degradation of organic contaminants, enabling compliance with environmental discharge standards.
Biogas and Energy Recovery Projects
As governments and businesses look to diversify their renewable energy portfolios, CSTR systems offer a proven method to generate methane-rich biogas from organic waste. This aligns with global sustainability goals and carbon neutrality targets.
Key Considerations for Applying CSTR Reactors with Enamel Tanks
For CSTR systems to function optimally across different waste treatment scenarios, several factors must be considered during design and implementation.
Feedstock Characteristics and Pre-treatment
The consistency, biodegradability, and chemical composition of the feedstock determine reactor sizing and mixing requirements. Pre-treatment methods—such as shredding, homogenization, or pH balancing—can improve reactor efficiency.
Temperature and pH Control
Maintaining mesophilic or thermophilic conditions is critical for anaerobic digestion. CSTRs should be equipped with heating systems, insulation, and automatic monitoring controls to keep environmental parameters within the ideal range.
Mixing Mechanism Design
Effective stirring prevents sedimentation and ensures the uniform distribution of microbes and nutrients. Mechanical mixers must be selected based on tank volume, feedstock viscosity, and energy efficiency.
Gas Collection and Safety Systems
For reactors used in biogas production, proper gas sealing and collection mechanisms must be integrated. Safety measures such as pressure relief valves, flame arrestors, and monitoring systems are essential.
Enamel Tank Specifications
The tank’s enamel coating should meet international standards for chemical resistance and structural integrity. Center Enamel’s GFS tanks are NSF/ANSI 61 certified, ISO 9001 compliant, and resistant to UV, acid, and alkali exposure.
Regulatory Compliance and Site Adaptation
Local environmental regulations, climate conditions, and land availability must be factored into the reactor’s design. Modular CSTR units can be adapted for various installation environments, from rural farms to dense industrial zones.
Why Center Enamel is the Leading Choice for CSTR Reactor Projects
Center Enamel brings decades of engineering expertise and innovation to every project, providing turnkey CSTR solutions that are efficient, reliable, and tailored to specific treatment goals.
Industry Leadership in Enamel Technology
With over 30 years of experience and successful installations in over 90 countries, Center Enamel is a recognized global expert in glass-fused-to-steel tank solutions. Our enamel coating technology ensures long-term performance under harsh chemical conditions.
Complete CSTR System Engineering
We provide fully integrated CSTR systems, including enamel tanks, mixers, heating systems, control panels, and gas collection infrastructure. This one-stop approach simplifies project management and ensures system compatibility.
Flexible Design and Modular Construction
Our bolted tanks allow for fast installation and easy scalability. Whether for a pilot plant or a large-scale municipal facility, our solutions can grow alongside client needs, saving costs and time in future expansions.
Strict Quality Control and International Certification
Center Enamel tanks are manufactured under rigorous quality standards and certified to meet global norms, including ISO, NSF, WRAS, and AWWA. This ensures that our solutions meet the highest expectations for safety and performance.
Global Reach with Local Service
We maintain a strong international presence through partnerships and service centers worldwide. This enables us to provide localized support, technical guidance, and post-installation maintenance anywhere in the world.
Sustainability-Focused Innovation
Center Enamel continuously invests in R&D to improve energy efficiency, reduce carbon emissions, and optimize waste-to-energy conversion. Our isothermal and adiabatic CSTR configurations are specifically engineered to meet today’s environmental challenges.
With the increasing demand for scalable and sustainable waste treatment systems, Center Enamel’s continuous CSTR reactors with enamel assembly tanks offer a high-performance, cost-effective, and eco-friendly solution for diverse industries. Designed to endure and built to adapt, these systems are setting new benchmarks in reliable and efficient wastewater treatment.