Large-Scale CSTR Reactors Engineered for Industrial Applications
In the world of industrial water treatment, efficient processing of wastewater is a critical concern, especially for industries with high organic waste loads, such as chemical production, food processing, and pharmaceutical manufacturing. Center Enamel, a leading provider of innovative water treatment solutions, has engineered large-scale Continuous Stirred Tank Reactors (CSTR) to address the unique challenges of industrial wastewater management. These reactors are designed for continuous operation, making them ideal for large-scale industrial applications where consistency and reliability are essential. By offering efficient anaerobic digestion processes, CSTR reactors help industries manage their wastewater while also recovering valuable biogas for energy production.
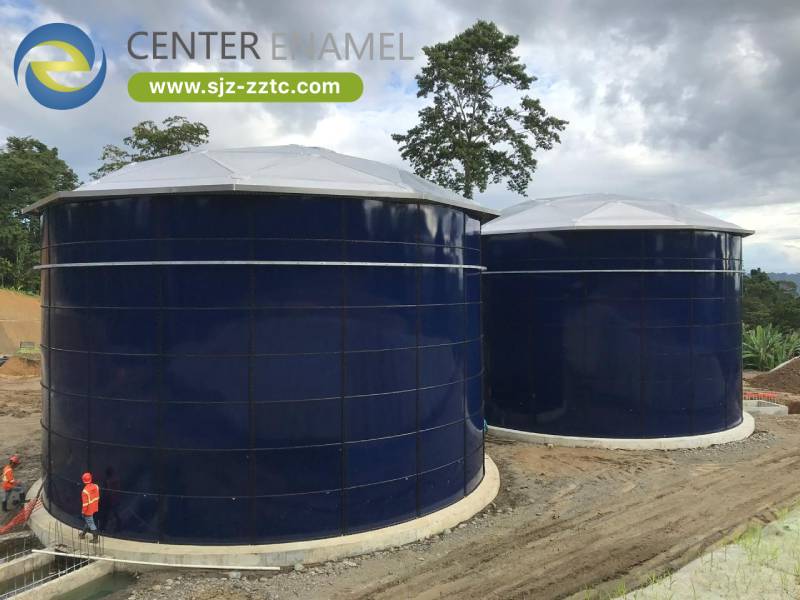
Advantages of Large-Scale CSTR Reactors for Industrial Applications
CSTR reactors are highly effective for treating wastewater in industrial settings, and they provide several distinct advantages when applied at a large scale. These benefits ensure that industries can achieve efficient, reliable, and sustainable wastewater treatment, contributing to both environmental protection and operational efficiency.
Continuous and Stable Operation:
One of the key advantages of CSTR reactors is their continuous operation, which allows them to process large volumes of wastewater consistently over extended periods. This is particularly important in industries that generate high quantities of wastewater, such as chemical, food, and textile industries. The continuous flow ensures that organic matter is constantly broken down, minimizing the risk of system interruptions and maximizing throughput.
Biogas Recovery and Energy Generation:
One of the standout features of CSTR reactors is their ability to generate biogas during the anaerobic digestion process. This biogas, primarily composed of methane, can be captured and utilized as a renewable energy source. For industrial facilities, this means a reduction in energy costs, as biogas can be used for heating, electricity generation, or as a fuel source for industrial processes, making the system not only environmentally sustainable but also cost-effective.
Lower Energy and Operational Costs:
Unlike aerobic systems that require significant energy input for aeration, CSTR reactors rely on anaerobic processes that require less energy. This makes CSTR systems more energy-efficient, particularly in large-scale industrial applications. Additionally, the reactor’s ability to generate biogas further offsets energy costs, making the system more cost-effective over time.
Importance of CSTR Reactors in Industrial Wastewater Treatment
In industrial applications, efficient wastewater treatment is crucial not only for environmental protection but also for ensuring compliance with local regulations and industry standards. CSTR reactors play an essential role in meeting these needs, offering a solution that supports sustainability and operational efficiency.
Compliance with Environmental Regulations:
As environmental regulations become stricter globally, industries must ensure that their wastewater treatment systems meet the required standards for effluent quality. CSTR reactors are designed to reduce the organic pollutants in wastewater to acceptable levels, helping industries comply with local and international environmental standards. This is crucial for preventing contamination of local water sources and reducing the overall environmental impact of industrial operations.
Supporting Sustainable Industrial Practices:
With growing awareness of environmental sustainability, industries are increasingly focused on reducing their ecological footprint. CSTR reactors support sustainable practices by providing an efficient means of treating wastewater while generating renewable energy. This helps industries contribute to global sustainability goals by reducing the consumption of non-renewable resources and minimizing the release of harmful pollutants into the environment.
Energy Independence and Cost Reduction:
As industries continue to face rising energy costs, the ability to generate biogas through CSTR reactors offers a significant advantage. By utilizing the biogas produced during anaerobic digestion, industrial operations can reduce their reliance on external energy sources. This contributes to energy independence and lowers operational costs, creating a more resilient and sustainable industrial ecosystem.
Key Factors to Consider When Using CSTR Reactors in Industrial Applications
While CSTR reactors offer numerous benefits for large-scale industrial applications, certain factors must be considered to ensure their optimal performance. These considerations can help industries maximize the effectiveness of the reactors and avoid operational issues.
Wastewater Characteristics:
The composition of wastewater can vary significantly across different industries. Factors such as the concentration of organic matter, pH levels, temperature, and the presence of toxic substances must be carefully considered when designing a CSTR reactor system. Analyzing these characteristics ensures that the reactor can be tailored to meet the specific treatment needs of the industry.
System Integration and Space Requirements:
Large-scale CSTR reactors require sufficient space for installation and integration into existing infrastructure. Industries must plan for the physical space needed for the reactor, along with necessary support equipment such as pumps, biogas collection systems, and heating units. Proper integration with existing wastewater systems is crucial for minimizing downtime during installation and ensuring smooth operation after commissioning.
Temperature Control and Stability:
The efficiency of anaerobic digestion processes is highly dependent on temperature. CSTR reactors must maintain an optimal temperature range to ensure the proper growth and activity of microorganisms. In industrial settings where temperature fluctuations can occur, it may be necessary to include heating or cooling systems to maintain stability. Monitoring and adjusting the temperature within the reactor is key to ensuring efficient performance.
Why Choose Center Enamel for Large-Scale CSTR Reactor Solutions?
Center Enamel is an industry leader in the design and manufacture of large-scale CSTR reactors, offering customized solutions for a wide range of industrial applications. Our expertise in wastewater treatment ensures that our reactors meet the highest standards of efficiency, sustainability, and reliability. Here’s why Center Enamel is the ideal choice for large-scale industrial applications:
High-Quality Materials and Construction:
Our CSTR reactors are built with the highest quality materials to ensure durability, corrosion resistance, and long-term performance. The reactors are designed to withstand the harsh conditions typically found in industrial environments, offering a reliable solution for wastewater treatment.
Customized Designs:
At Center Enamel, we understand that each industrial operation is unique. Our engineers work closely with clients to design customized CSTR reactors that are perfectly suited to their specific needs. Whether it's handling high organic loads or optimizing biogas production, we offer solutions that meet the exact requirements of your operation.
Comprehensive Support:
From design and installation to operation and maintenance, Center Enamel provides full-service support for our CSTR reactor systems. Our expert team is available to assist with system integration, commissioning, and troubleshooting, ensuring that your reactor operates at peak efficiency throughout its lifecycle.
By choosing Center Enamel’s large-scale CSTR reactors, industries can achieve a more sustainable and cost-effective approach to wastewater treatment while also benefiting from the generation of renewable energy. Our advanced reactor systems provide reliable solutions for a wide range of industrial applications, making them the perfect choice for companies looking to optimize their environmental performance and reduce operational costs.