Leading Pharmaceutical Wastewater Treatment Anaerobic Digestion Process Contractor|Center Enamel
The global pharmaceutical industry, a cornerstone of public health, is under increasing scrutiny for its environmental footprint, particularly concerning its wastewater discharge. Pharmaceutical wastewater is notoriously complex, often characterized by high Chemical Oxygen Demand (COD), diverse organic compounds, fluctuating pH, and sometimes the presence of recalcitrant or inhibitory substances like antibiotics and solvents. If left untreated or inadequately managed, this effluent can pose significant threats to aquatic ecosystems, public health, and lead to stringent regulatory penalties. As pharmaceutical manufacturers worldwide commit to enhanced sustainability and responsible production, there is an urgent need for advanced, robust, and cost-effective treatment solutions. The Pharmaceutical wastewater Treatment Anaerobic Digestion Process stands out as a powerful and proven technology, capable of effectively breaking down complex organic pollutants while simultaneously generating valuable renewable energy.
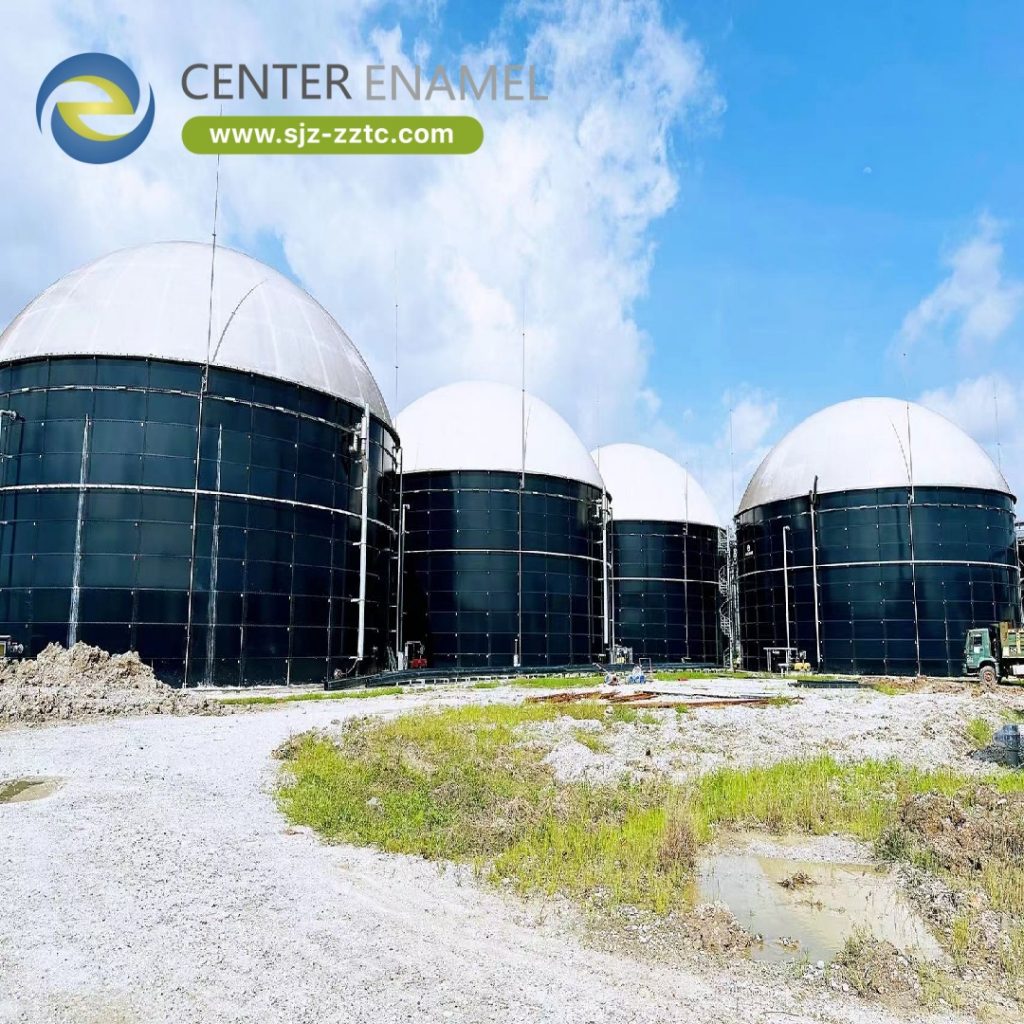
At the forefront of environmental engineering for the pharmaceutical sector, Shijiazhuang Zhengzhong Technology Co., Ltd (Center Enamel) is globally recognized as a Leading Pharmaceutical wastewater Treatment Anaerobic Digestion Process Contractor. As a distinguished China Pharmaceutical wastewater Treatment Anaerobic Digestion Process Contractor, Center Enamel brings unparalleled expertise in Glass-Fused-to-Steel (GFS) tank manufacturing and comprehensive environmental project execution. We specialize in designing, constructing, and commissioning advanced anaerobic digestion systems meticulously tailored for diverse pharmaceutical manufacturing facilities across the globe. Our extensive experience, unwavering commitment to precision engineering, and proven success in delivering high-performance, cost-effective solutions firmly establish us as the premier partner for pharmaceutical producers striving for rigorous environmental compliance, energy self-sufficiency, and enhanced operational sustainability.
The Intricate Challenges of Pharmaceutical Wastewater
Pharmaceutical wastewater presents a unique and often challenging profile compared to other industrial effluents. Its complexity arises from:
Variable Composition: Depending on the specific drug synthesis, formulation, and cleaning processes, the wastewater can contain a wide array of organic compounds, solvents, active pharmaceutical ingredients (APIs), and excipients.
High and Variable Organic Load (COD/BOD): While highly concentrated in COD, the biodegradability can vary significantly, with some compounds being readily digestible and others being recalcitrant or even inhibitory to biological processes.
Presence of Inhibitory Substances: Antibiotics, disinfectants, solvents, and heavy metals can be present, which are toxic to microorganisms and can disrupt conventional biological treatment systems.
Fluctuating pH: Cleaning-in-Place (CIP) procedures, fermentation processes, and chemical reactions can lead to wide and rapid pH swings, requiring robust pH neutralization.
Color and Odor: Some pharmaceutical wastewaters exhibit distinct colors or strong odors that require effective removal.
Temperature Variations: Process water discharge can lead to varying temperatures that need to be managed for optimal anaerobic digestion.
Successfully addressing these intricate challenges, while simultaneously generating valuable resources, is where the Pharmaceutical wastewater Treatment Anaerobic Digestion Process provides immense value, and where Center Enamel offers its leading expertise.
Center Enamel's Advanced Pharmaceutical Wastewater Treatment Anaerobic Digestion Process
As a Leading Pharmaceutical wastewater Treatment Anaerobic Digestion Process Contractor, Center Enamel employs a meticulously designed, multi-stage approach that optimizes the entire Pharmaceutical wastewater Treatment Anaerobic Digestion Process for maximum efficiency, biogas production, and stringent environmental compliance. Our solutions are engineered based on extensive experience and the superior performance of our Glass-Fused-to-Steel (GFS) tank technology.
Specialized Pre-treatment for Pharmaceutical Effluent: Robust pre-treatment is paramount for pharmaceutical wastewater to mitigate challenges posed by high and variable organic loads, inhibitory substances, and pH fluctuations, ensuring stable and efficient digester performance. Our customized solutions include:
Equalization and Homogenization: Employing our highly durable GFS tanks as equalization basins. Their superior chemical resistance to diverse pharmaceutical compounds, excellent hygiene, and robust structural integrity ensure a consistent and buffered feed to the digester, which is vital for stable anaerobic conditions and handling shock loads from batch processes or CIP cycles.
pH Neutralization and Temperature Conditioning: Automated systems for precisely adjusting pH to optimal levels for anaerobic microbes and managing influent temperature to suit the chosen digestion process (mesophilic or thermophilic), crucial for stability when dealing with varying influent characteristics.
Physical-Chemical Pre-treatment: Depending on the wastewater characteristics, this may involve coagulation, flocculation, or adsorption to remove suspended solids, color, or specific inhibitory compounds before biological treatment.
High-Efficiency Anaerobic Digester Design for Pharmaceutical Applications: The anaerobic digester is the core of the Pharmaceutical wastewater Treatment Anaerobic Digestion Process. Center Enamel engineers select, design, and construct robust, high-performance reactors specifically suited for the unique characteristics of pharmaceutical wastewater:
High-Rate Anaerobic Reactors (UASB, IC, EGSB): These are particularly well-suited for high-strength, soluble or easily hydrolyzable organic loads common in many pharmaceutical wastewaters. They offer compact footprints, high organic loading rates, and excellent COD removal efficiencies, crucial for industries often located in densely populated areas with limited space.
Continuous Stirred Tank Reactors (CSTR): May be chosen for pharmaceutical operations with higher suspended solids, or if co-digestion with other compatible organic waste streams is planned, ensuring thorough mixing and optimal contact between microbes and substrate.
Glass-Fused-to-Steel (GFS) Tanks: The Superior Digester Vessel: Our proprietary GFS tanks are the cornerstone of our anaerobic digesters for pharmaceutical plants. As a pioneer in developing advanced enameling technology, Center Enamel offers tanks with:
Unmatched Corrosion Resistance: The vitrified glass coating provides an inert, impermeable barrier against the highly corrosive nature of pharmaceutical wastewater (due to acids, alkalis, and complex organic compounds) and the produced biogas, ensuring integrity and a long operational life with minimal maintenance.
Exceptional Gas-Tightness: Precision engineering and advanced sealants guarantee minimal biogas leakage, maximizing recovery for energy use and preventing fugitive methane emissions. This is crucial for both energy efficiency and environmental compliance.
Hygiene and Easy Maintenance: The smooth, inert surface prevents bio-fouling and simplifies cleaning, promoting a healthy microbial environment, which is vital for continuous industrial operations requiring high standards.
Rapid, Modular Construction: GFS tanks offer significantly faster installation times compared to concrete, minimizing disruption to sensitive pharmaceutical production schedules. Their modularity allows for flexible design layouts and and efficient future expansion.
Comprehensive Biogas Recovery and On-site Energy Utilization: A major economic and environmental advantage of the Pharmaceutical wastewater Treatment Anaerobic Digestion Process is Biogas Recovery. Center Enamel integrates complete systems for capturing, purifying, and beneficially utilizing this valuable renewable energy directly within the pharmaceutical facility:
Biogas Collection and Storage: Secure, gas-tight GFS tanks are essential for efficient biogas collection and buffering.
Biogas Purification: Systems for removing impurities like hydrogen sulfide (H2S) and moisture, producing a cleaner, higher-quality fuel that protects downstream equipment. For pharmaceutical applications, additional purification may be necessary depending on the biogas composition and intended use.
Energy Conversion: We commonly integrate Combined Heat and Power (CHP) units, allowing pharmaceutical plants to generate their own electricity and heat from biogas. This can significantly reduce reliance on grid power and fossil fuels, lower energy costs for process heating (e.g., sterilization, distillation), and enhance the plant's energy independence and economic viability. Biogas can also be directly used as boiler fuel.
Post-treatment and Final Effluent Polishing: The treated effluent from the Pharmaceutical wastewater Treatment Anaerobic Digestion Process is significantly cleaner, but due to the stringent discharge standards for pharmaceutical wastewater, further polishing is almost always required for final discharge or water reuse.
Secondary/Tertiary Treatment (Aerobic Polishing/Advanced Treatment): Typically involves aerobic processes like activated sludge, Membrane Bioreactors (MBR), or Moving Bed Biofilm Reactors (MBBR) for residual COD/BOD and nutrient removal. Advanced oxidation processes (AOPs) or activated carbon adsorption may be employed for recalcitrant compounds or micropollutant removal.
Sludge Volume and Odor Reduction: Anaerobic digestion significantly reduces the volume of sludge requiring further handling and minimizes foul odors, improving the pharmaceutical plant's overall environmental footprint.
Center Enamel: Your Full-Service China Pharmaceutical Wastewater Treatment Anaerobic Digestion Process Contractor with Global Expertise
Center Enamel's distinction as a Leading Pharmaceutical wastewater Treatment Anaerobic Digestion Process Contractor is built upon our integrated "Full Chain Service" EPC (Engineering, Procurement, and Construction) model. We offer a seamless, single-point-of-responsibility solution that ensures project success from conceptualization to operational reality:
Expert Consultation & Process Design: Our highly experienced environmental engineers and process specialists provide in-depth technical consultation, developing customized anaerobic digestion schemes tailored to the specific characteristics, volumes, and peak loads of your pharmaceutical wastewater. Our designs strictly adhere to international engineering standards, including AWWA D103-09, OSHA, and ISO/EN28765.
High-Capacity Production & Certified Quality: Our state-of-the-art manufacturing facilities ensure rapid and precise fabrication of GFS tanks and other components. Our commitment to quality is validated by a comprehensive suite of international certifications, including ISO 9001, ISO 14001, ISO 45001, NSF/ANSI 61, WRAS, CE/EN1090, ISO 28765, and FDA compliance.
Global Installation & Commissioning Expertise: With more than 30,000 engineering projects completed in over 100 countries, our skilled installation teams ensure swift, safe, and quality-controlled on-site assembly and meticulous commissioning. We guarantee that the entire anaerobic digestion system operates efficiently and reliably from day one.
Responsive After-Sales Support: Our robust global sales and service network provides rapid response for professional and efficient after-sales support, ensuring the long-term reliability and peak performance of your pharmaceutical wastewater treatment plant.
Proven Success: Driving Sustainability in the Global Pharmaceutical Industry
Center Enamel's extensive project portfolio showcases our unparalleled experience as a China Pharmaceutical wastewater Treatment Anaerobic Digestion Process Contractor with a proven global track record, consistently delivering high-performance solutions for diverse industrial clients, including those with challenging organic waste streams relevant to pharmaceutical production:
High-Strength Industrial Wastewater Projects: Our experience with various high-strength industrial organic wastewaters (e.g., chemical, food & beverage, and other complex industrial effluents) demonstrates our adaptability to diverse organic compounds and inhibitory substances often found in pharmaceutical wastewater.
Large-Scale Biogas Production Facilities: Our involvement in significant biogas production facilities showcases our capability to handle substantial organic loads and generate considerable renewable energy, directly applicable to the energy needs of pharmaceutical manufacturing.
International Industrial Wastewater Projects: Our global footprint includes projects in countries with stringent environmental regulations and high-tech industrial standards, underscoring our ability to deliver compliant and efficient anaerobic digestion solutions applicable to pharmaceutical manufacturing facilities worldwide.
These numerous and varied projects underscore Center Enamel's unwavering commitment to engineering excellence and our proven capability as a Leading Pharmaceutical wastewater Treatment Anaerobic Digestion Process Contractor, delivering robust, efficient, and sustainable solutions that empower pharmaceutical producers to meet stringent environmental regulations, reduce operational costs, enhance energy independence, and contribute to a greener, more responsible pharmaceutical industry globally.
Partner for Sustainable Pharmaceutical Manufacturing
In the global pursuit of responsible and sustainable manufacturing, the Pharmaceutical wastewater Treatment Anaerobic Digestion Process is an indispensable tool. Center Enamel, with its pioneering GFS tank technology, deep process expertise, comprehensive EPC capabilities, and stellar global reputation, is uniquely positioned to be your trusted partner. We offer not just solutions, but tailored, high-performance anaerobic digestion systems that optimize pharmaceutical wastewater management, generate valuable renewable energy, ensure compliance, and provide long-term economic and environmental advantages for your pharmaceutical production operations, anywhere in the world.