Reliable CSTR Reactors with Fusion Bonded Epoxy Tanks for Long-Term Waste Treatment Solutions
Continuous Stirred Tank Reactors (CSTR) are a vital part of industrial and municipal wastewater treatment processes, particularly in anaerobic digestion systems where organic waste must be efficiently broken down. With increasing demands for durable, corrosion-resistant, and cost-effective systems, the integration of Bonded Epoxy (FBE) tanks into CSTR systems represents a major technological advancement. As a global leader in the field of wastewater storage and treatment, Center Enamel provides high-performance CSTR reactors built with fusion-bonded epoxy tanks, offering long-term waste treatment solutions for municipalities and industries alike.
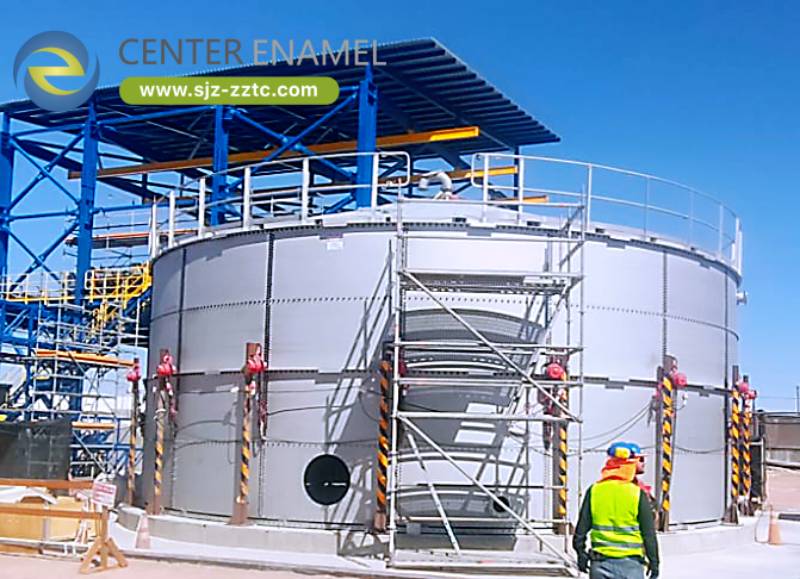
Key Advantages of CSTR Reactors with Fusion Bonded Epoxy Tanks
CSTR reactors are known for their robust design and steady-state operation, but when combined with fusion-bonded epoxy tanks, their durability and performance are taken to the next level. Here are the core advantages:
Superior Corrosion Resistance
Fusion bonded epoxy coatings create an impermeable barrier between the tank wall and the contents inside, offering excellent resistance to corrosion from acidic or chemically aggressive waste. This is critical for long-term performance, especially in anaerobic digestion processes that generate hydrogen sulfide and other corrosive gases.
Enhanced Tank Longevity
Compared to traditional tank materials, such as carbon steel or concrete, fusion-bonded epoxy tanks have a significantly longer lifespan due to their resistance to both internal and external corrosive elements. This greatly reduces maintenance frequency and lifecycle costs.
Stable Reactor Performance
CSTR reactors function best under continuous, uniform conditions. The smooth, non-stick surface of epoxy-coated tanks minimizes buildup and scaling, ensuring better mixing efficiency and heat distribution throughout the reactor. This supports consistent microbial activity and enhances the biodegradation process.
Ease of Installation and Maintenance
Fusion-bonded epoxy tanks are pre-fabricated and modular in design, which allows for quick on-site assembly. Maintenance is also simpler thanks to the easy-to-clean surface and resistance to fouling, reducing downtime and labor costs.
Energy Efficiency and Sustainability
The efficient operation of the reactor, combined with the insulation benefits of the epoxy coating, means less energy is required to maintain the optimal temperature for digestion. This translates to lower energy consumption and improved sustainability performance.
The Role of CSTR Reactors in Wastewater Treatment Across Key Industries
CSTR reactors with fusion-bonded epoxy tanks offer unique benefits across a variety of sectors, making them critical infrastructure for sustainable waste management.
Municipal Wastewater Treatment
For urban areas, wastewater treatment plants require reliable, scalable, and long-lasting solutions. CSTR reactors process high organic loads efficiently, and the fusion-bonded epoxy tank ensures corrosion resistance against sewage sludge and biogas by-products. Their robust performance ensures compliance with strict environmental discharge regulations.
Agricultural and Livestock Waste Management
The agricultural sector generates large amounts of biodegradable waste from animal manure and crop residues. CSTR reactors allow for the controlled digestion of this organic matter, converting it into valuable biogas and nutrient-rich digestate. The use of epoxy tanks further ensures that high ammonia and volatile fatty acids don’t degrade the system’s performance over time.
Food and Beverage Industry
Industries such as dairy processing, breweries, and canning operations discharge high-COD (chemical oxygen demand) wastewater. A CSTR system with epoxy-lined tanks ensures efficient degradation of organic matter and reduces the chemical footprint before discharge or reuse, all while withstanding the variable composition of industrial effluents.
Chemical and Pharmaceutical Manufacturing
These industries often deal with effluents containing corrosive and complex chemical compounds. The fusion-bonded epoxy lining acts as a strong protective layer, ensuring reactor integrity even when treating aggressive waste streams.
Key Considerations When Implementing CSTR Reactors with Epoxy Tanks
To ensure that the CSTR reactors with fusion-bonded epoxy tanks deliver maximum efficiency and longevity, several operational and design considerations must be taken into account.
Waste Characteristics
Understanding the nature of the waste stream is critical. The chemical composition, organic load, temperature, and pH of the wastewater all impact how the CSTR reactor is designed and operated. For highly corrosive or high-strength waste, epoxy tanks provide much-needed protection.
Temperature Control
Maintaining mesophilic or thermophilic temperatures is essential for optimal digestion. FBE tanks offer excellent insulation properties, helping to maintain consistent reactor temperatures, but it’s still important to have monitoring systems and heat exchangers in place.
Retention Time and Reactor Volume
Determining the correct hydraulic retention time (HRT) is vital for effective digestion. The large-capacity modular tanks allow for scaling the reactor size to match treatment goals, whether for small-scale municipal systems or large industrial complexes.
Mixing System Efficiency
Uniform mixing inside the reactor ensures equal distribution of temperature, nutrients, and microorganisms. Epoxy-coated internal surfaces reduce the friction that can hinder mixing and reduce energy efficiency. Proper mixer design should complement the tank’s smooth surface for optimal flow dynamics.
Gas Handling and Safety
For anaerobic digestion systems, the biogas produced needs to be safely stored or utilized. FBE tanks maintain gas-tight conditions, preventing leakage and ensuring safety. Additional gas collection, flare, or energy recovery systems should be considered depending on project goals.
Why Center Enamel Is the Preferred Choice for Epoxy-Coated CSTR Reactor Systems
As one of the global leaders in tank manufacturing and wastewater treatment engineering, Center Enamel offers complete turnkey solutions tailored to each project’s unique needs.
Industry-Leading Fusion Bonded Epoxy Technology
Center Enamel’s epoxy coating process meets and exceeds international standards, including AWWA D103, NSF/ANSI 61, and ISO 9001. Our tanks are designed to handle harsh environments with exceptional chemical resistance and mechanical strength.
Fast, Efficient Installation
Our modular tank design means quicker construction timelines with minimal disruption. The on-site bolted installation system reduces labor and equipment costs, enabling rapid deployment, particularly in regions with labor constraints or remote access challenges.
Sustainability and Innovation at Our Core
We are committed to helping industries and municipalities reduce their environmental impact. By enabling energy recovery through biogas utilization and minimizing chemical discharge, our CSTR systems align with global sustainability goals and carbon reduction strategies.
Center Enamel’s reliable CSTR reactors, enhanced with fusion-bonded epoxy tank technology, represent the future of long-term, high-efficiency waste treatment. Whether you’re seeking corrosion resistance, consistent performance, or scalable capacity, our solutions offer unmatched value across multiple sectors within the chemical and environmental industries.