Reliable IC Reactors for Effective Cheese Wastewater Management
As the global demand for dairy products continues to grow, cheese production has witnessed a significant rise. However, one of the major environmental challenges faced by the dairy industry is the effective treatment of cheese wastewater, which is characterized by high organic loads, suspended solids, fats, proteins, and lactose. Shijiazhuang Zhengzhong Technology Co., Ltd. (Center Enamel), a trusted global supplier of wastewater treatment solutions, offers IC Reactors (Internal Circulation Reactors) that provide a reliable and sustainable solution for cheese wastewater management. With over 30 years of experience in tank system engineering and anaerobic technology integration, Center Enamel ensures optimized treatment performance while helping clients meet regulatory and sustainability goals.
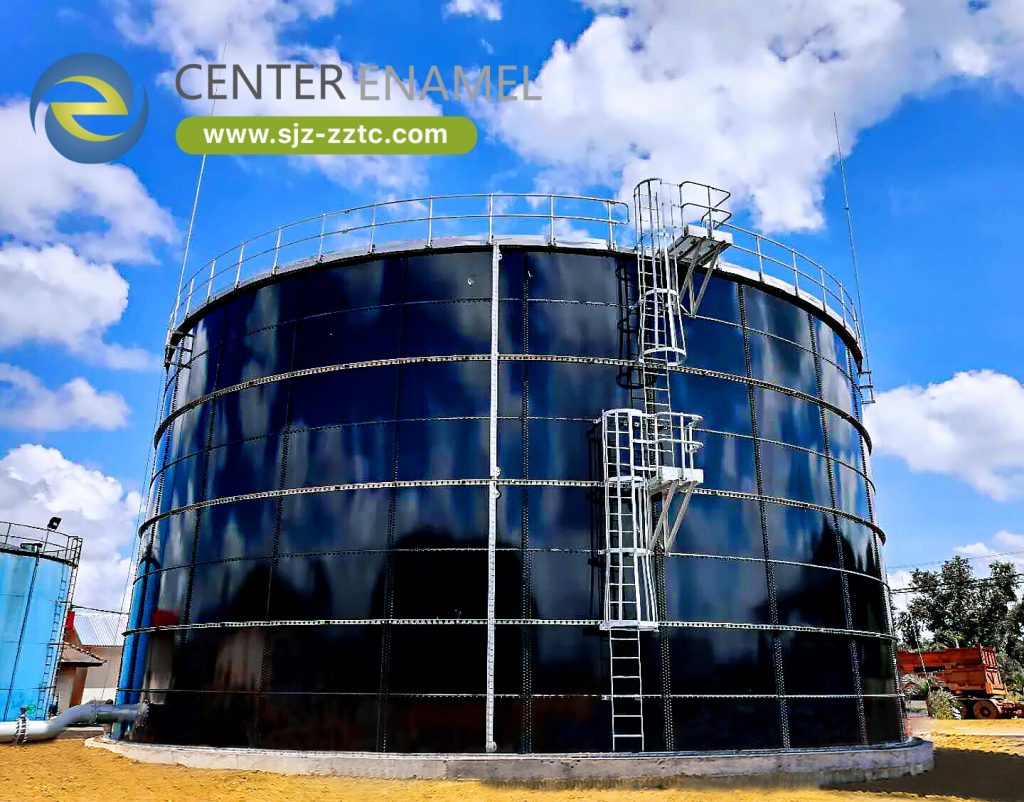
Distinct Advantages of IC Reactors for Cheese Wastewater Treatment
IC Reactors are among the most advanced anaerobic digestion systems available today, offering unparalleled performance for high-strength industrial wastewater like that from cheese production. The structure and operational design of IC Reactors provide several technical and operational advantages:
High Organic Load Capacity: IC Reactors are capable of treating wastewater with COD concentrations exceeding 20,000 mg/L, making them ideal for cheese production facilities that generate high-strength effluent.
Energy Recovery through Biogas: The anaerobic process transforms organic pollutants into biogas, primarily methane, which can be used on-site for thermal energy or electricity generation, thus reducing the factory’s carbon footprint.
Compact and Modular Design: Compared to other anaerobic systems, IC Reactors occupy a smaller land area. Their modularity allows for easy capacity expansion to accommodate increased wastewater volumes during peak production seasons.
Low O&M Costs: Due to low energy requirements, minimal sludge production, and the absence of chemical additives, operational costs are significantly reduced.
Hydraulic and Process Stability: IC Reactors are designed to manage hydraulic shocks and variable influent loads, ensuring consistent performance even during fluctuations in cheese production.
Minimal Maintenance Downtime: With a fully enclosed design and advanced automation, the reactor requires limited human intervention and minimal downtime for maintenance.
These features make IC Reactors a preferred choice for dairy facilities aiming for high-efficiency wastewater treatment and energy recovery.
Significance of IC Reactor Systems in Cheese Wastewater Management
In cheese manufacturing, every kilogram of cheese produces wastewater, which includes process wash water, whey by-products, and cleaning agents. Such wastewater poses serious environmental risks if not treated properly. The application of IC Reactor systems in cheese wastewater treatment is crucial for several reasons:
Environmental Protection and Regulatory Compliance: Countries around the world have implemented stringent discharge regulations concerning Chemical Oxygen Demand (COD), Biochemical Oxygen Demand (BOD), Total Suspended Solids (TSS), and nutrients such as nitrogen and phosphorus. The IC Reactor system reduces COD and BOD levels by over 90%, ensuring regulatory compliance and protection of local water bodies.
Resource Recovery and Reuse: The conversion of organic matter into biogas not only reduces pollution but also transforms waste into a valuable energy source. Recovered methane gas can be used to generate electricity or heat, powering boilers or even the treatment system itself.
Sustainability in Dairy Processing: With increasing pressure from stakeholders to embrace sustainability, cheese producers are adopting circular economy practices. IC Reactors supports zero-waste and low-carbon initiatives, contributing to corporate social responsibility goals.
Odor Control and Hygiene: Anaerobic treatment conducted in sealed tanks prevents odor emissions and provides a more hygienic facility environment—an essential factor for food-grade production areas.
Scalability for Future Needs: Whether managing wastewater from a small cheese plant or a large-scale production unit, the IC Reactor system can be designed for future scalability, allowing manufacturers to expand operations without overhauling their treatment infrastructure.
Reduced Load on Secondary Treatment: Efficient anaerobic digestion via the IC Reactor significantly lowers the organic load on subsequent aerobic treatment units, leading to improved overall system efficiency and lower energy consumption.
The integration of IC Reactors into cheese manufacturing wastewater management not only improves plant sustainability but also enhances brand reputation in an increasingly environmentally conscious market.
Technical and Operational Considerations for IC Reactor Integration
To ensure the success of IC Reactor application in cheese wastewater projects, several critical technical and operational aspects must be considered. These include:
Microbial Culture and Start-Up:
Introduce appropriate anaerobic biomass to initiate digestion.
Gradual loading and pH control are essential to avoid acidification during the initial phases.
Biogas Collection and Safety:
Install gas collection domes, piping, and safety devices such as pressure relief valves and gas monitoring systems.
Biogas can be purified and stored or directly used in gas engines, boilers, or combined heat and power (CHP) units.
Effluent Handling:
Post-treatment options such as aerobic polishing, membrane filtration, or nutrient removal may be incorporated depending on discharge standards or water reuse objectives.
Automation and Monitoring:
Integrate SCADA systems and sensors for real-time monitoring of pH, temperature, biogas yield, and organic loading rate.
Use predictive maintenance tools to ensure long-term operational reliability.
By considering these factors, cheese manufacturers can achieve optimal IC Reactor performance while minimizing risks and ensuring long-term environmental compliance.
Why Center Enamel is the Ideal Partner for IC Reactor Projects in the Dairy Sector
Center Enamel is not only a supplier but also a strategic partner dedicated to helping clients meet their wastewater treatment and sustainability goals. Our leadership in providing high-performance IC Reactors for cheese wastewater treatment is built upon the following strengths:
Rich Industry Experience: With a track record of successful projects across over 100 countries, Center Enamel brings unmatched knowledge of wastewater treatment processes specific to the dairy and food industries.
Custom-Engineered Systems: Every IC Reactor system is tailored based on the client’s specific wastewater profile, project size, and future expansion plans.
Durable Enamel-Coated Steel Tanks: Our reactors utilize premium Glass-Fused-to-Steel tanks that offer outstanding corrosion resistance, 30+ years of service life, and low maintenance costs. The enamel coating provides strong adhesion, smooth surface finish, and excellent chemical resistance.
Global Project References: Center Enamel has completed numerous IC Reactor installations for dairy clients worldwide, including in Europe, the Middle East, Southeast Asia, and South America. Our clients range from small-scale dairy cooperatives to multinational cheese producers.
Certification and Quality Assurance: Center Enamel adheres to international quality standards, with certifications including ISO 9001, NSF/ANSI 61, ISO 14001, and ISO 45001. Our equipment complies with CE, WRAS, and other regional codes, ensuring global applicability.
By choosing Center Enamel’s IC Reactor technology, cheese manufacturers gain access to a reliable, scalable, and environmentally responsible solution for managing high-strength dairy wastewater.