Reliable IC Reactors for Sustainable Brewing Wastewater Treatment Operations
In the brewing industry, sustainability has become more than a buzzword—it’s a necessity. As breweries grow and demand for craft and industrial beer increases, so does the volume of wastewater they generate. Brewing wastewater, characterized by high concentrations of organic matter, suspended solids, and variable pH levels, poses significant environmental challenges. To meet stricter regulations and corporate environmental targets, breweries are increasingly turning to anaerobic digestion technologies. Among these, the Internal Circulation (IC) Reactor stands out for its reliability, efficiency, and sustainability. As a leading provider in wastewater treatment solutions, Shijiazhuang Zhengzhong Technology Co., Ltd (Center Enamel) is at the forefront of deploying advanced IC Reactor systems tailored to the brewing industry’s needs.
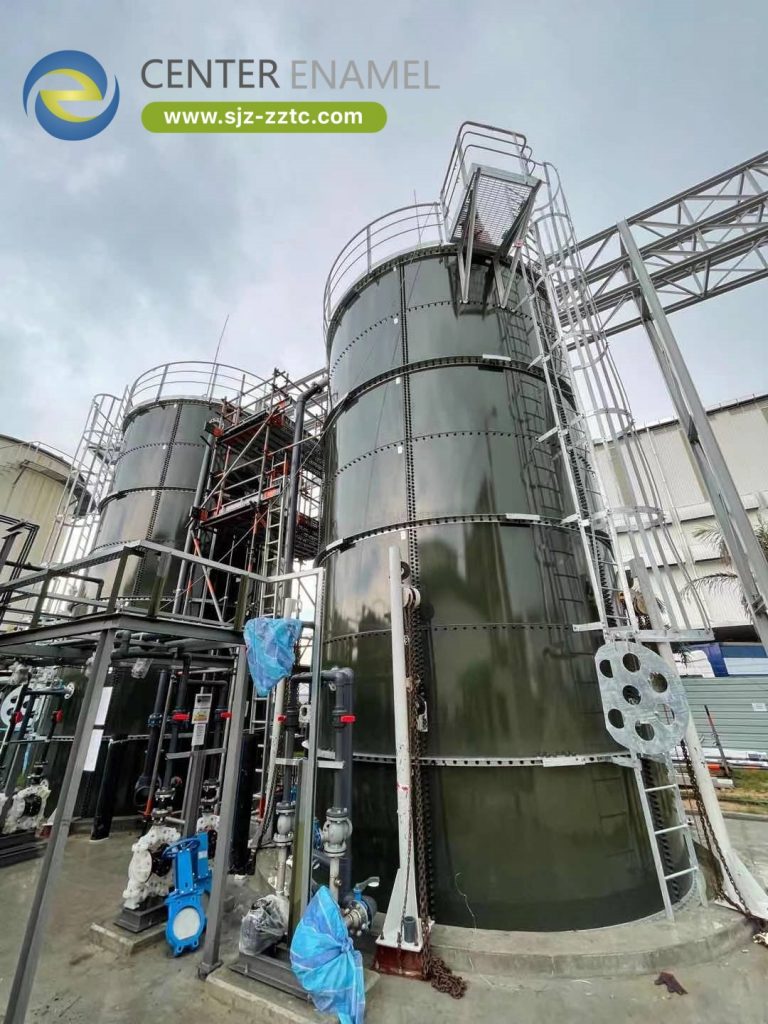
The Technical Advantages of IC Reactors in Brewing Wastewater Treatment
The IC Reactor is a type of high-rate anaerobic reactor known for its compact structure, high efficiency, and robust adaptability to fluctuating influent loads. This makes it especially suited for the dynamic nature of brewing wastewater, which can vary in COD (Chemical Oxygen Demand), BOD (Biochemical Oxygen Demand), pH, and temperature based on the production schedule.
Key advantages of Center Enamel’s IC Reactors include:
High Loading Rates: IC Reactors handle high organic loading rates, significantly reducing footprint requirements compared to traditional anaerobic reactors such as UASB systems.
Internal Recirculation: The dual-sludge bed and internal circulation loop enhance biomass contact and maximize digestion efficiency without the need for external energy inputs.
Energy Recovery: IC Reactors generate biogas during the anaerobic digestion process. In brewing operations, this methane-rich gas can be captured and used for process heating, thereby reducing energy costs and improving energy independence.
Stable Performance: Even under fluctuating load conditions, IC Reactors maintain stable operations due to their efficient mixing and biomass retention capabilities.
Low Sludge Production: The anaerobic process results in minimal excess sludge, reducing post-treatment sludge handling and associated costs.
These features make IC Reactors an attractive solution for breweries that aim to lower their operational costs and improve environmental performance simultaneously.
Importance of IC Reactors in the Brewing Industry’s Wastewater Strategy
The brewing industry generates wastewater at multiple stages—mashing, lautering, boiling, fermentation, and cleaning. This effluent contains sugars, alcohols, proteins, hop residues, and detergents that require advanced treatment before release or reuse.
The implementation of IC Reactors has become crucial in brewery wastewater management due to several sector-specific demands:
Sustainability Goals: With growing pressure to adopt green manufacturing practices, breweries increasingly invest in technologies like IC Reactors that support carbon footprint reduction and resource recovery.
Production Scalability: As breweries expand production, wastewater volumes grow accordingly. IC Reactors offer scalable configurations that can be adapted to both small craft breweries and large industrial beer manufacturers.
Water Reuse Initiatives: Treated effluent from IC Reactors can be reused in non-potable applications such as cleaning or cooling, helping breweries meet water conservation goals.
By enabling efficient biological treatment and biogas recovery, IC Reactors are integral to brewing operations that prioritize both productivity and environmental responsibility.
Design Considerations for IC Reactor Integration in Brewery Applications
Successful implementation of an IC Reactor system in a brewery requires thoughtful design and operational planning. Center Enamel tailors each project to the unique requirements of the client, ensuring maximum treatment efficiency and operational safety. Some of the critical factors considered include:
Influent Characteristics: Brewing wastewater varies in pH, temperature, COD/BOD, and total suspended solids. IC Reactors need pre-treatment systems like screening, equalization, and pH adjustment to ensure stable loading conditions.
Hydraulic Retention Time (HRT): Determining the appropriate HRT is essential to optimize organic degradation while maintaining reactor size and efficiency.
Sludge Management: Though IC Reactors produce less sludge than aerobic systems, sludge handling and disposal must still be planned, particularly in facilities with limited land availability.
Biogas Handling Systems: Center Enamel integrates biogas collection, storage, and utilization systems, ensuring safe handling and maximum energy recovery.
Automation and Monitoring: Advanced IC Reactors by Center Enamel are equipped with automated monitoring systems to track key parameters like pH, temperature, flow rate, and biogas production, ensuring optimized operation and rapid fault detection.
These design and operational parameters ensure long-term performance and reliability, supporting breweries’ goals of cost-effective and sustainable wastewater treatment.
Center Enamel’s Competitive Edge in IC Reactor Technology
With over 30 years of experience, Center Enamel is a trusted partner for wastewater treatment systems worldwide. The company’s IC Reactor solutions stand out due to several core strengths:
Proven Project Experience: Center Enamel has successfully delivered IC Reactor systems for diverse clients, including breweries, distilleries, dairy processing plants, and food manufacturing industries across Asia, Europe, and Africa.
High-Quality Materials: The company uses glass-fused-to-steel (GFS) tanks for its IC Reactor structures. These tanks offer excellent corrosion resistance, longevity, and easy installation.
Customization and Scalability: Center Enamel provides modular IC Reactor systems designed to meet varying capacity requirements, from small-scale breweries to high-output commercial operations.
R&D and Technical Support: The company invests in research and innovation, continuously improving the performance and automation of its reactors. Technical support includes design, installation guidance, commissioning, and after-sales service.
Environmental and Energy Efficiency Focus: Center Enamel’s IC Reactors not only ensure regulatory compliance but also help breweries reduce energy use and greenhouse gas emissions, aligning with global sustainability goals.
Additionally, Center Enamel emphasizes rapid construction timelines and cost-effective installation, ensuring minimal disruption to ongoing operations. The pre-assembled tank and reactor components simplify logistics and reduce on-site work.
Expanding Role of IC Reactors in Sustainable Brewing Operations
As sustainability evolves from a strategic initiative to an operational necessity, breweries across the globe are recognizing the vital role of IC Reactors. These systems not only ensure environmental compliance but also contribute to energy efficiency, water reuse, and corporate social responsibility.
Some forward-thinking breweries are even integrating IC Reactors into circular economy models—using biogas from anaerobic digestion to power brewing operations or local communities and treating wastewater for irrigation or utility water. This shift from waste management to resource recovery is accelerating, and IC Reactors are at the heart of this transition.
Center Enamel’s IC Reactor systems are designed with this future in mind. With durable construction, intelligent automation, and a commitment to environmental performance, Center Enamel supports breweries in building a more sustainable and cost-effective future.