Scalable IC Reactor Systems for Various Dairy Wastewater Volumes
In the dairy industry, one of the biggest challenges lies in the effective treatment of dairy wastewater, which is typically high in organic load, fats, and suspended solids. With rising environmental standards and sustainability becoming a priority, the need for efficient, compact, and cost-effective treatment solutions has grown rapidly. This is where IC Reactor (Internal Circulation Reactor) systems step in — providing a high-rate anaerobic solution specifically designed for industries such as dairy processing. At the forefront of delivering advanced IC Reactor technologies is Shijiazhuang Zhengzhong Technology Co., Ltd. (Center Enamel), a global provider of high-performance storage and treatment systems tailored for industrial and municipal applications.
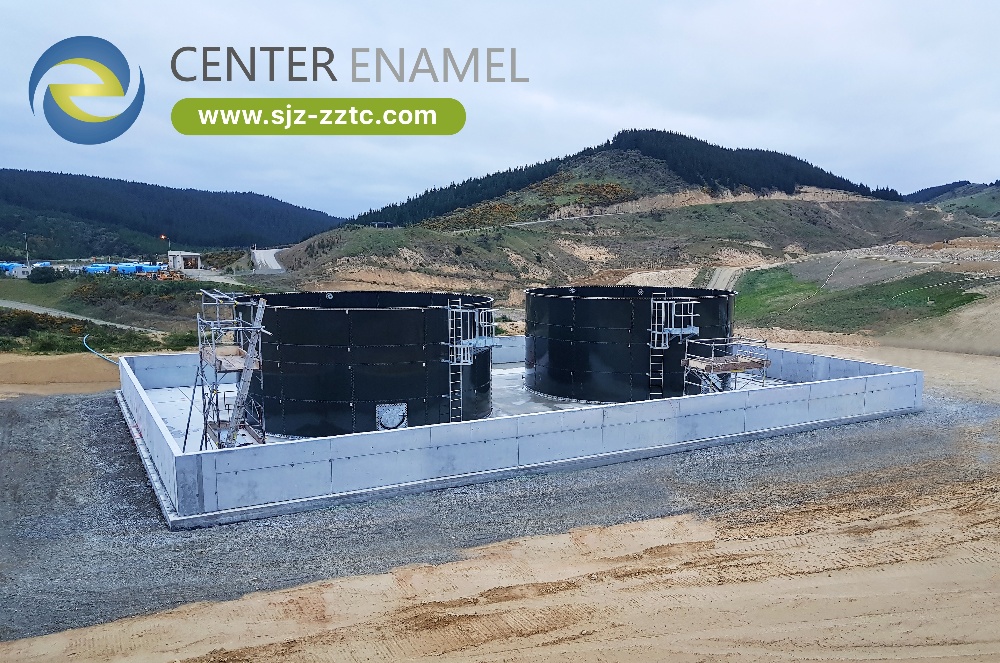
Why IC Reactor Systems Are Ideal for Dairy Wastewater Treatment
The unique characteristics of dairy wastewater, such as high Chemical Oxygen Demand (COD), fluctuating pH, and nutrient imbalances, demand advanced treatment systems that can handle variability without sacrificing efficiency. IC Reactors, as a type of upflow anaerobic sludge blanket (UASB) reactor with enhanced internal circulation, offer several core advantages:
High Organic Loading Capacity: IC Reactors can treat high-COD dairy wastewater effectively, making them ideal for milk, cheese, and yogurt production facilities.
Compact Footprint: With their vertical design and internal circulation mechanism, IC Reactors require less space compared to conventional anaerobic digesters.
Two-Stage Digestion: The design separates the reactor into two upflow chambers, enabling a two-phase digestion process that maximizes biogas production and ensures higher treatment efficiency.
Energy Recovery Through Biogas: A significant advantage of IC Reactors is their ability to capture biogas from dairy effluents, converting waste into renewable energy.
Stable Operation: Their modularity and robust design enable consistent performance even with highly variable effluent flows and compositions — common in dairy facilities.
These features combine to deliver an energy-efficient and environmentally friendly solution for dairies of all sizes.
Importance of IC Reactor Systems in the Dairy Industry
As global dairy production expands and environmental regulations tighten, the role of IC Reactor systems in the dairy sector becomes even more critical. Here’s why they’ve gained prominence:
Regulatory Compliance: Dairy factories must meet increasingly stringent discharge limits for COD, BOD, and TSS. IC Reactors ensure these limits are achieved consistently.
Operational Cost Savings: By converting organic matter into biogas, IC systems significantly lower electricity and fuel costs, improving the bottom line for dairy producers.
Scalability for Various Dairy Volumes: Whether it’s a small-scale artisanal plant or a large industrial milk processor, IC Reactor systems can be customized to match treatment capacity requirements — from hundreds to thousands of cubic meters per day.
Circular Economy Contribution: Biogas generated from IC Reactors can be used onsite for boilers or electricity, aligning with the dairy industry’s push towards circular resource use.
Improved Public Perception: Environmentally responsible operations improve brand value and consumer trust, especially in food and beverage industries where sustainability is now a key market differentiator.
The integration of IC Reactors into dairy wastewater treatment reflects an industry-wide shift toward energy self-sufficiency, responsible water management, and long-term economic resilience.
Considerations When Implementing IC Reactors for Dairy Wastewater
Despite their numerous benefits, selecting and deploying an IC Reactor system for dairy wastewater must be approached with technical precision. Here are several critical considerations:
Influent Characterization: A detailed understanding of dairy effluent (e.g., COD, BOD, fats, proteins) is essential for accurate system sizing and reactor design.
Temperature Control: Anaerobic digestion processes are temperature-sensitive. Facilities must maintain mesophilic or thermophilic conditions for optimal microbial activity.
Hydraulic Retention Time (HRT): Designing the correct HRT is vital to allow sufficient digestion while minimizing reactor volume and costs.
Fat and Oil Content Management: Dairy wastewater is often rich in fats, which may inhibit digestion. Pre-treatment or fat traps might be needed before the IC Reactor stage.
Sludge Handling: Sludge generation is minimal but not negligible. Proper sludge management strategies should be incorporated to ensure long-term operational stability.
Startup Period: Seeding the reactor with acclimated anaerobic sludge can significantly shorten startup times and reduce risk.
Gas Handling Systems: To fully benefit from biogas generation, gas-tight systems, gas scrubbers, and energy recovery units should be integrated from the outset.
Careful planning and expert consultation are crucial for dairy producers to realize the full benefits of IC Reactor systems.
Why Choose Center Enamel for Your Dairy Wastewater Treatment Project?
Center Enamel has earned a global reputation as a reliable partner in providing IC Reactor systems and integrated wastewater treatment solutions. Our commitment to quality, innovation, and sustainability ensures our clients achieve optimal performance and environmental compliance. Here's what sets us apart:
Rich Project Experience: Center Enamel has completed hundreds of anaerobic digestion projects across industries, including numerous dairy processing plants in Asia, Europe, and the Middle East.
Advanced Materials and Design: Our IC Reactors are often integrated with Glass-Fused-to-Steel or Fusion Bonded Epoxy tanks, offering superior corrosion resistance, long service life, and easy assembly.
Modular and Scalable Solutions: Our systems are designed to grow with your operations. Whether your dairy is expanding or adjusting to seasonal production changes, our IC Reactors adapt seamlessly.
Turnkey Services: From process design and manufacturing to installation and commissioning, we provide end-to-end solutions tailored to customer needs.
Global Technical Support: Our engineering and after-sales support teams are always ready to assist—no matter where your facility is located.
Compliance with International Standards: All our products comply with international codes such as AWWA D103-09, ISO 9001, and NSF certifications, ensuring safety and reliability.
By choosing Center Enamel, dairy producers gain not only a robust treatment solution but also a trusted partner committed to long-term environmental and economic outcomes.