Selecting the Right IC Reactor for Your Pharmaceutical Wastewater Storage Tank Needs
The pharmaceutical industry, crucial for global health, generates substantial and complex wastewater from API and medicinal product manufacturing. Characterized by diverse organic compounds, solvents, antibiotics, and varying nutrient levels, this effluent poses significant environmental and public health risks if inadequately treated. Traditional aerobic methods often struggle with this complexity, demanding more efficient solutions. Advanced anaerobic digestion, particularly utilizing the IC reactor, has emerged as a promising alternative for treating high-strength pharmaceutical wastewater, offering broad organic degradation, energy recovery potential, a compact design, and reduced sludge production. Selecting the right IC reactor is vital for effective and sustainable treatment outcomes.
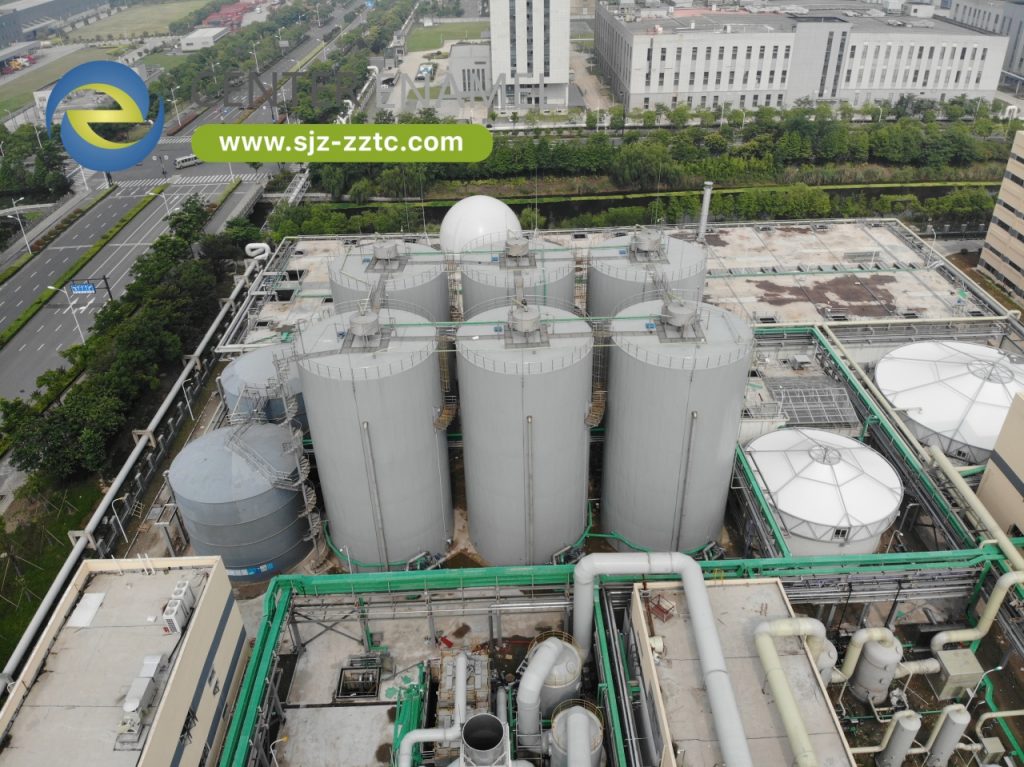
Understanding Pharmaceutical Wastewater Characteristics and Specific Treatment Challenges
Pharmaceutical wastewater presents a unique set of challenges due to its diverse and often complex composition. Key characteristics and treatment challenges include:
- Complex Organic Load: Characterized by a wide array of organic compounds, including APIs, intermediates, solvents, and excipients, often with varying biodegradability.
- Presence of Pharmaceutical Residues: Even in low concentrations, these residues can have ecological and potential human health implications.
- Antibiotic Content: The presence of antibiotics in wastewater can contribute to the development and spread of antibiotic-resistant bacteria.
- Chemical Inhibitors: Certain process chemicals and solvents can inhibit the biological activity of microorganisms in wastewater treatment systems.
- Variable pH and Salinity: Manufacturing processes can result in wastewater with fluctuating pH and salinity levels, which can impact biological treatment efficiency.
- Disinfection Byproducts: Pre-treatment disinfection processes may generate disinfection byproducts that need to be addressed.
- Stringent Regulatory Requirements: The pharmaceutical industry is subject to stringent environmental regulations regarding the discharge of wastewater, often requiring specific monitoring and removal of pharmaceutical substances.
Meeting these complex challenges necessitates a wastewater treatment technology that is not only capable of degrading a broad spectrum of organic pollutants but also robust enough to handle variable wastewater characteristics and potentially address the presence of specific pharmaceutical compounds. The selected technology should also align with sustainability goals, minimizing energy consumption and waste generation.
Center Enamel's IC Reactor Technology: A Tailored Solution for Pharmaceutical Wastewater Treatment
Center Enamel, a global leader in advanced anaerobic digestion technologies, offers its high-performance Internal Circulation (IC) reactor as a sophisticated and adaptable solution for the efficient and sustainable treatment of pharmaceutical wastewater. The IC reactor's unique two-stage design and robust operation make it particularly well-suited to handle the complex organic load and potential inhibitory substances present in this type of effluent.
The IC reactor's tall, slender vertical configuration optimizes the anaerobic digestion process by creating distinct zones for the sequential breakdown of complex organic matter. The internal circulation, driven by the biogas produced in the lower stage, ensures efficient mixing, enhanced contact between microorganisms and the diverse substrates, and the development of a resilient and highly active granular sludge. This design promotes the degradation of a wide range of organic compounds, even those that may be challenging for conventional anaerobic systems.
The Science Behind IC Reactor Technology for Pharmaceutical Wastewater Treatment
The Internal Circulation (IC) reactor employs a highly optimized two-stage vertical anaerobic digestion process to effectively treat complex organic wastewater like that from pharmaceutical manufacturing:
Acidogenic Zone (Lower Compartment): The pharmaceutical wastewater enters the bottom of the IC reactor, where a diverse community of acidogenic bacteria rapidly breaks down complex organic molecules (including some pharmaceutical compounds) into simpler volatile fatty acids (VFAs), hydrogen, and carbon dioxide. The biogas produced in this initial stage creates a gas lift effect, propelling the liquid upwards through an internal riser.
Internal Circulation and Enhanced Mixing: At the top of the lower compartment, the biogas disengages, and the partially treated liquid flows downwards through an internal downcomer into the upper compartment. This internal recirculation ensures thorough mixing, promoting uniform distribution of VFAs and maximizing contact between the diverse microbial consortia and the various organic substrates present in the pharmaceutical wastewater.
Methanogenic Zone (Upper Compartment): In the upper compartment, a specialized community of methanogenic archaea converts the VFAs, hydrogen, and carbon dioxide into methane-rich biogas. The specific microbial populations within this zone can adapt to the presence of certain pharmaceutical compounds, potentially contributing to their partial degradation. The biogas produced in this stage is also efficiently collected.
Effluent Discharge and Granular Sludge Retention: The treated effluent, with a significantly reduced organic load and potentially altered concentrations of pharmaceutical residues, is discharged from the top of the reactor. The unique hydraulic conditions and internal circulation within the IC reactor promote the formation and retention of dense, well-settling granular sludge. This highly active and diverse microbial biomass ensures a stable and robust treatment process capable of handling the complex and variable nature of pharmaceutical wastewater.
Key Advantages of Center Enamel's IC Reactor for Pharmaceutical Wastewater Treatment:
- Broad Spectrum Organic Compound Degradation: The two-stage anaerobic process within the IC reactor, with its diverse microbial communities, can effectively degrade a wider range of organic compounds, including some that may be recalcitrant to traditional anaerobic digestion.
- Enhanced Tolerance to Inhibitory Substances: The robust granular sludge and optimized operating conditions within the IC reactor can provide increased tolerance to certain chemical inhibitors that may be present in pharmaceutical wastewater.
- Potential for Partial Degradation of Pharmaceutical Residues: While complete mineralization of all pharmaceutical compounds may not always be achievable with anaerobic digestion alone, the IC reactor can contribute to the partial breakdown and transformation of some pharmaceutical residues, potentially reducing their environmental impact.
- Significant Biogas Production for Energy Recovery: The high organic content of pharmaceutical wastewater often translates to significant biogas production within the IC reactor. This renewable energy source can be harnessed for heating, electricity generation, or other energy applications within the pharmaceutical facility, contributing to energy efficiency and cost savings.
- Compact Footprint for Space-Constrained Facilities: The vertical design and high treatment efficiency of the IC reactor result in a smaller land area requirement compared to many conventional treatment systems, which is particularly advantageous for pharmaceutical manufacturing plants often located in industrial areas with limited space.
- Stable and Resilient Operation Under Variable Conditions: The robust granular sludge and efficient internal mixing within the IC reactor contribute to a stable and resilient treatment process capable of handling fluctuations in wastewater flow and composition, which can occur in pharmaceutical manufacturing.
- Reduced Sludge Production Minimizing Disposal Challenges: Anaerobic digestion generally produces significantly less excess sludge compared to aerobic treatment, reducing the volume of sludge requiring further processing and disposal, which is particularly important considering the potential presence of pharmaceutical residues in the sludge.
- Minimized Odor Emissions Ensuring a Better Working Environment: The enclosed design of the IC reactor effectively contains the anaerobic digestion process, minimizing the potential for unpleasant odor emissions associated with wastewater treatment, contributing to a better working environment for the pharmaceutical facility.
- Durability and Low Maintenance with GFS Technology: Center Enamel constructs its IC reactors using our renowned Glass-Fused-to-Steel (GFS) technology. This provides exceptional resistance to the corrosive chemicals often found in pharmaceutical wastewater, ensuring a long service life and minimizing maintenance requirements.
Integrating IC Reactors with Pharmaceutical Wastewater Storage Tank Needs
The successful implementation of IC reactor technology for pharmaceutical wastewater treatment necessitates the integration with appropriate storage tank systems to manage the various streams within the treatment process. Center Enamel's GFS tanks provide reliable and durable storage solutions for:
- Equalization Tanks: To buffer fluctuations in flow and composition of the raw pharmaceutical wastewater, ensuring a consistent feed to the IC reactor and optimizing its biological activity.
- Influent Storage Tanks: Providing temporary storage of raw wastewater before it enters the IC reactor, allowing for controlled feeding and potential pre-treatment adjustments.
- Sludge Storage Tanks: For the temporary storage of the stabilized sludge produced by the IC reactor, prior to dewatering, further treatment, or disposal in accordance with stringent regulations for pharmaceutical waste.
- Biogas Storage Tanks: Safely storing the biogas generated by the IC reactor, enabling its controlled utilization for energy production within the pharmaceutical facility, contributing to energy independence and cost reduction.
- Effluent Storage Tanks: Holding the treated effluent before discharge to a municipal sewer system or further advanced treatment stages, allowing for final quality checks and controlled release.
The chemical resistance and durability of Center Enamel's GFS tanks are particularly crucial for handling the potentially corrosive nature of pharmaceutical wastewater and its treatment byproducts. The modular design allows for customized tank sizes and configurations to meet the specific volume and layout requirements of pharmaceutical manufacturing plants.
Center Enamel: A Trusted Partner for Sustainable Pharmaceutical Wastewater Management
Center Enamel is dedicated to partnering with pharmaceutical companies worldwide to provide customized IC reactor solutions and integrated GFS storage tank systems that enable sustainable and cost-effective wastewater management. Our comprehensive expertise includes:
- Detailed Wastewater Characterization and Treatability Studies: We conduct thorough analyses of pharmaceutical wastewater to understand its specific characteristics and determine the optimal IC reactor design and operating parameters.
- Customized IC Reactor Design and Engineering: Our experienced engineering team designs IC reactor systems tailored to the specific needs of pharmaceutical wastewater treatment, considering the complex organic load and potential presence of specific compounds.
- High-Quality GFS Tank Manufacturing for Diverse Storage Needs: We manufacture durable and chemically resistant GFS tanks for equalization, influent storage, sludge storage, biogas storage, and effluent storage, ensuring the safe and reliable management of all wastewater streams.
- Integrated Biogas Handling and Utilization Systems: We provide comprehensive solutions for the safe and efficient collection, treatment, storage, and utilization of biogas generated by the IC reactor, maximizing energy recovery potential.
- Turnkey Project Management and Support: Center Enamel offers complete project management services, from initial consultation and feasibility studies to design, manufacturing, installation, commissioning, and ongoing technical support.
- Compliance with Stringent Industry Standards: Our GFS tanks and IC reactor systems are designed and manufactured to meet the highest international quality and safety standards, relevant to the pharmaceutical industry.