Why Choose IC Reactors for Sustainable Pharmaceutical Wastewater Treatment?
The pharmaceutical industry plays a crucial role in public health, producing life-saving medications and treatments. However, it also generates significant quantities of wastewater laden with complex organic pollutants, active pharmaceutical ingredients (APIs), and other hazardous substances. Effective treatment of pharmaceutical wastewater is necessary not only to protect the environment and human health but also to comply with stringent environmental regulations globally. As pharmaceutical manufacturing continues to scale, the need for advanced wastewater treatment technologies becomes more critical.
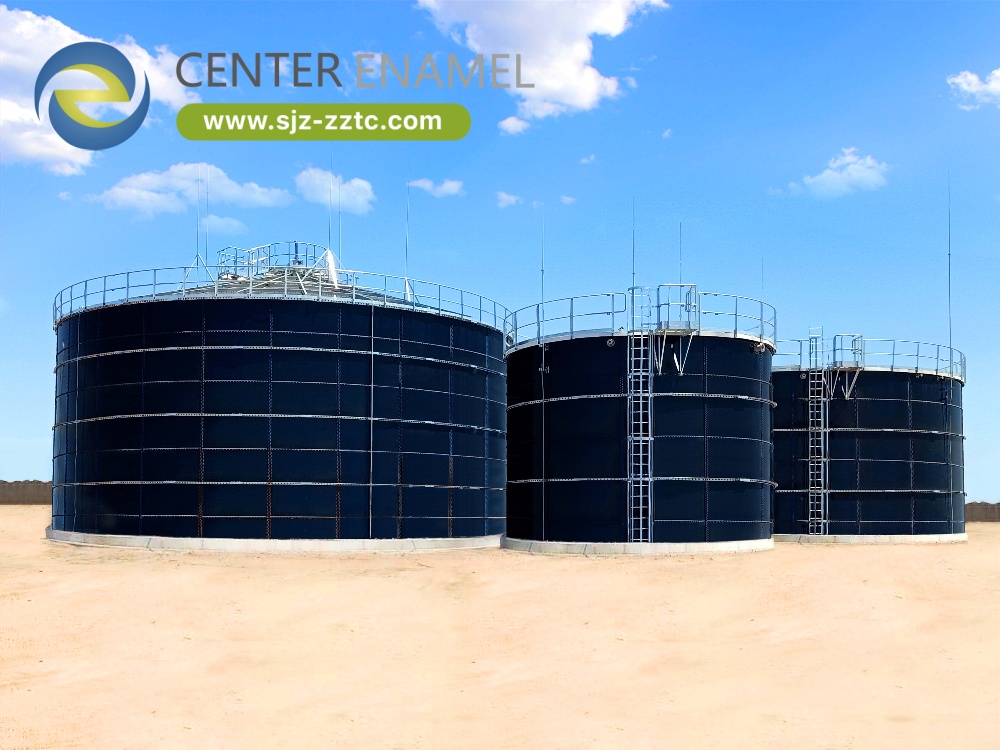
The Internal Circulation (IC) Reactor has emerged as a preferred technology among the various treatment solutions available due to its outstanding efficiency, sustainability, and adaptability. Shijiazhuang Zhengzhong Technology Co., Ltd (Center Enamel), as a leading provider of high-performance environmental solutions, offers IC Reactor systems that meet the rigorous demands of pharmaceutical wastewater treatment. With decades of expertise and innovation, Center Enamel provides IC Reactors designed for maximum performance and environmental compliance.
Key Advantages of IC Reactors for Pharmaceutical Wastewater
IC Reactors bring a range of technical advantages that make them highly suitable for handling the complex nature of pharmaceutical wastewater. These include:
1. High Tolerance to Complex Pollutants
IC Reactors are specifically designed to process high-strength wastewater, including that with high chemical oxygen demand (COD) and biological oxygen demand (BOD).
The pharmaceutical industry's effluent contains diverse compounds such as antibiotics, solvents, endocrine-disrupting chemicals, and residual APIs. IC Reactors offer robust degradation performance even under variable load conditions.
The layered sludge bed and enhanced microbial retention enable effective treatment of refractory organics.
2. Two-Stage Anaerobic Digestion for Increased Efficiency
The IC Reactor’s dual-stage reactor chamber design increases contact time between biomass and wastewater, allowing for more complete degradation of pollutants.
Internal circulation mechanisms improve mixing, promoting stable microbial activity and higher treatment efficiency.
Reduced sludge production compared to aerobic systems makes it more cost-effective in terms of sludge handling and disposal.
3. Minimal Footprint with Vertical Design
The compact, space-saving design of IC Reactors is ideal for pharmaceutical plants with limited land availability.
Despite their small footprint, these reactors deliver high volumetric loading rates and reduced hydraulic retention times.
4. Energy Recovery through Biogas Production
The anaerobic process within IC Reactors naturally produces biogas, primarily methane, as a byproduct.
This biogas can be captured and used for on-site energy generation, helping pharmaceutical facilities reduce energy costs and improve sustainability.
The energy-neutral or even energy-positive performance of IC systems enhances the economic feasibility of wastewater treatment projects.
5. Automation and Low Maintenance
Advanced control systems make IC Reactors easy to operate and manage.
Reduced mechanical complexity means fewer maintenance issues and long-term operational stability.
Real-time monitoring ensures system performance, with the flexibility to adjust to varying influent conditions.
The Critical Role of IC Reactors in Pharmaceutical Wastewater Management
The importance of IC Reactor deployment in pharmaceutical wastewater treatment is growing, driven by both environmental and economic factors.
1. Stricter Environmental Regulations Worldwide
Regulatory bodies across the world have increased scrutiny over the discharge of pharmaceutical effluents, with zero-tolerance policies toward untreated or partially treated discharges.
IC Reactors help pharmaceutical companies meet or exceed local and international effluent discharge standards.
Their ability to degrade micropollutants and persistent organic pollutants (POPs) aligns with global environmental safety requirements.
2. Meeting ESG and Sustainability Goals
Environmental, Social, and Governance (ESG) standards are now a key component of corporate strategy in the pharmaceutical sector.
IC Reactors contribute to sustainability by enabling waste-to-energy conversion and minimizing environmental footprints.
Facilities that adopt sustainable wastewater treatment systems like IC Reactors gain an advantage in brand image and investor trust.
3. Cost Optimization in Waste Management
Traditional aerobic treatment methods are energy-intensive and often less effective at managing high-strength wastewater.
IC Reactors drastically reduce operating costs by generating energy, minimizing sludge volumes, and lowering chemical requirements.
These reactors also reduce the need for tertiary treatment, further streamlining operational expenditures.
Key Considerations for Applying IC Reactors to Pharmaceutical Wastewater
Implementing IC Reactor technology for pharmaceutical wastewater treatment involves several critical factors:
1. Influent Characterization and Pretreatment
A detailed analysis of the influent’s chemical composition, pH, temperature, and flow rate is essential for reactor design.
Pretreatment, such as equalization or pH adjustment, may be required to stabilize feed conditions and enhance microbial activity.
2. Microbial Population and Adaptation
The successful operation of IC Reactors depends on the acclimatization of anaerobic microbial populations to the specific contaminants present in pharmaceutical wastewater.
Seeding with granular anaerobic sludge or adaptation periods may be necessary for consistent reactor performance.
3. Odor Control and Gas Management
Although anaerobic processes are typically odor-neutral, appropriate gas sealing and venting systems are crucial in pharmaceutical environments.
Gas treatment systems for hydrogen sulfide (H₂S) or volatile organic compounds (VOCs) should be integrated as needed.
Why Choose Center Enamel for IC Reactor Systems?
Center Enamel stands out as a premier supplier of IC Reactor systems tailored for pharmaceutical wastewater treatment due to the following strengths:
1. Proven Engineering and Design Capabilities
With over 30 years of experience, Center Enamel has delivered anaerobic digestion systems to over 100 countries.
The company’s design team customizes each reactor based on detailed wastewater characterization, process needs, and site constraints.
2. Glass-Fused-to-Steel Technology for Reactor Tanks
Center Enamel’s IC Reactors are constructed using high-quality glass-fused-to-steel tanks, which offer excellent corrosion resistance and long service life.
These tanks are easy to install and maintain, even under aggressive chemical and biological environments typical of pharmaceutical wastewater.
3. International Certifications and Quality Standards
Center Enamel’s products comply with ISO, NSF, WRAS, and AWWA standards, ensuring their suitability for critical environmental applications.
The reactors are designed and manufactured under European and American standards, meeting global project requirements.
4. End-to-End Project Support
From initial consultation to post-installation maintenance, Center Enamel offers full-service project support.
Technical training, operational guidance, and on-site supervision ensure seamless commissioning and long-term performance.
5. Global References in the Pharmaceutical Industry
Center Enamel has supplied IC Reactor systems to numerous pharmaceutical companies globally, earning a reputation for reliability and technological excellence.
Case studies demonstrate consistent performance in removing complex contaminants and achieving regulatory compliance.
6. Commitment to Innovation and Sustainability
The company continually invests in R&D to enhance reactor performance, improve biogas recovery, and reduce environmental impacts.
Its sustainable solutions align with circular economy principles and green manufacturing initiatives.